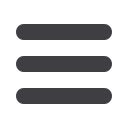
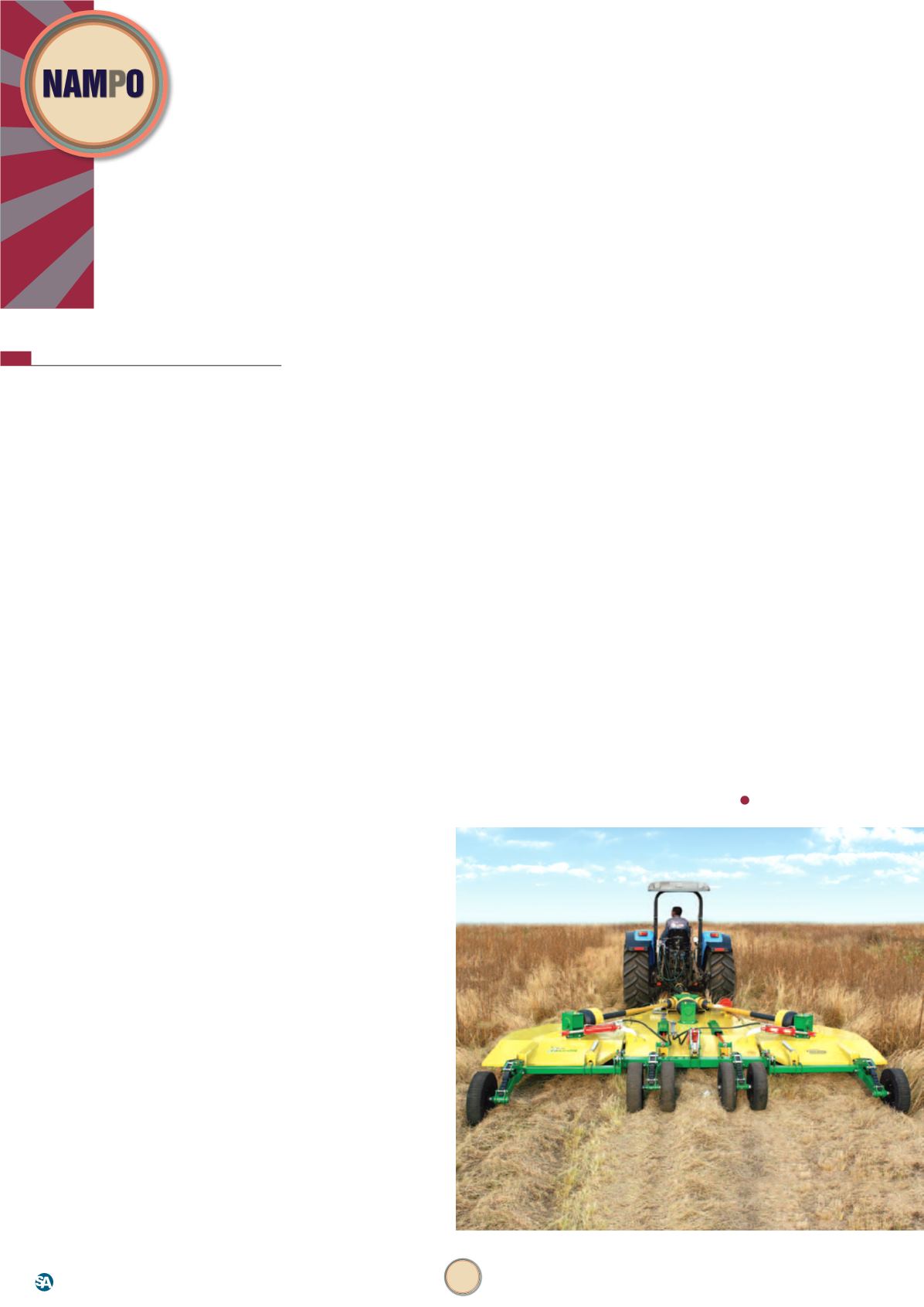
Graan|Grain
www.nampo.co.za22
F
alcon has become known in the agricultural industry in
South Africa as the benchmark for quality, durability and
safety of locally manufactured rotary cutters. As a compa-
ny, we stand firmly behind the slogan for the brand: ‘Falcon
stands the test of time, generation after generation’.
When referring to our implements, many will say ‘they
never break’, while others say ‘if it’s a Falcon, it just goes on and
on and on’. It is clear that we have built a very strong reputation
amongst our customers and competitors of reliability and durability.
We look at some of the factors that contribute to our ‘built to last’
implements.
Design and testing
Our implements are uniquely and expertly designed and built to
cope with the tough South African conditions. New implements
are rigorously tested for long periods and designs are adjusted and
perfected to meet stringent standards for long-term reliability.
Fabrication
Implements are manufactured from top-quality steel plate, suitably
reinforced with angle and channel iron which are stitch welded to
reduce distortions and stress fractures. 45 degree gusseted bends
are used to ensure maximum strength and side panels can be raised
or lowered to adjust the cutting height according to the requirement.
The heads of the bolts securing the panel are countersunk into
hexagonal recesses, so that only one spanner is required for height
adjustments. The side panels are protected by steel skid runners.
The topmast, which connects to the tractor’s top-link, is mounted on
bushes and connected to the rear of the implement by galvanised
HT steel chains. This flexible linkage allows the rotary cutter to follow
the ground contours. The lower linkage points are of the clevis type,
with loose pins, on the implements of 1,5 m and wider. The smaller
implements have fixed pins on the lower hitch-points.
Metal treatment and painting
All manufactured parts are subjected to a five-tank acid bath clean-
ing and phosphate treatment process. The primer paint coat is then
applied by complete immersion in a paint tank, which allows the
paint to reach all closed sections and recesses and behind all gus-
sets. All open seams are then sealed with a special sealant to protect
the implement from moisture, before the final enamel colour coat is
applied. All fasteners, chains, shackles and pins are electroplated
to guard against corrosion.
The Falcon gearbox
One of the secrets of the success of the rotary cutters is that the
F50, F60 and F80 series are fitted with locally manufactured heavy-
duty and extra heavy-duty gearboxes. These gearboxes, entirely
constructed by us, have proved to have a long, trouble-free life in
any operation, as they are specially designed both to withstand the
extraordinary working conditions encountered in Africa and to
absorb the higher power being produced by the new-generation
tractors coming into the market. The F50 and F80 have a warranty
period of three years and the F60 for two years against faulty manu-
facture. Because they are locally manufactured, these parts are also
easily and quickly available.
Drive shafts
All implements are supplied with appropriate, fully guarded PTO
shafts. Torque-limiting slip-clutches are supplied where specified.
Optional over-run or freewheel clutches can be supplied if required.
Listen and adapt
Part of the company’s pledge to our customers is that we will listen.
We understand that our success is based on what our customers be-
lieve exceptional service and quality to be, not what we believe it to
be. As a business, we are focused on receiving and listening to feed-
back, and in turn, improving our designs and fabrications to ensure
the implements get better and better.
Through our authorised dealer network, we also supply
spare parts for all implements. We are the exclusive supplier of all
Falcon original and Amazone spare parts, ensuring that wearing
parts can be replaced quickly and efficiently, reducing down time
of the implement.
Manufacturing implements for an increasingly competitive
market, where price is a major factor for the producer, is no easy
feat. The Falcon difference is that the implements are built to last
and stand the test of time, generation after generation. Visit us at the
NAMPO Harvest Day at stand E1 and stand E20.
Amanda Lock
on behalf of Falcon
The Falcon F60/450 Flexwing Slasher.
Implements
built to stand the test of time
P
2019
Product
information